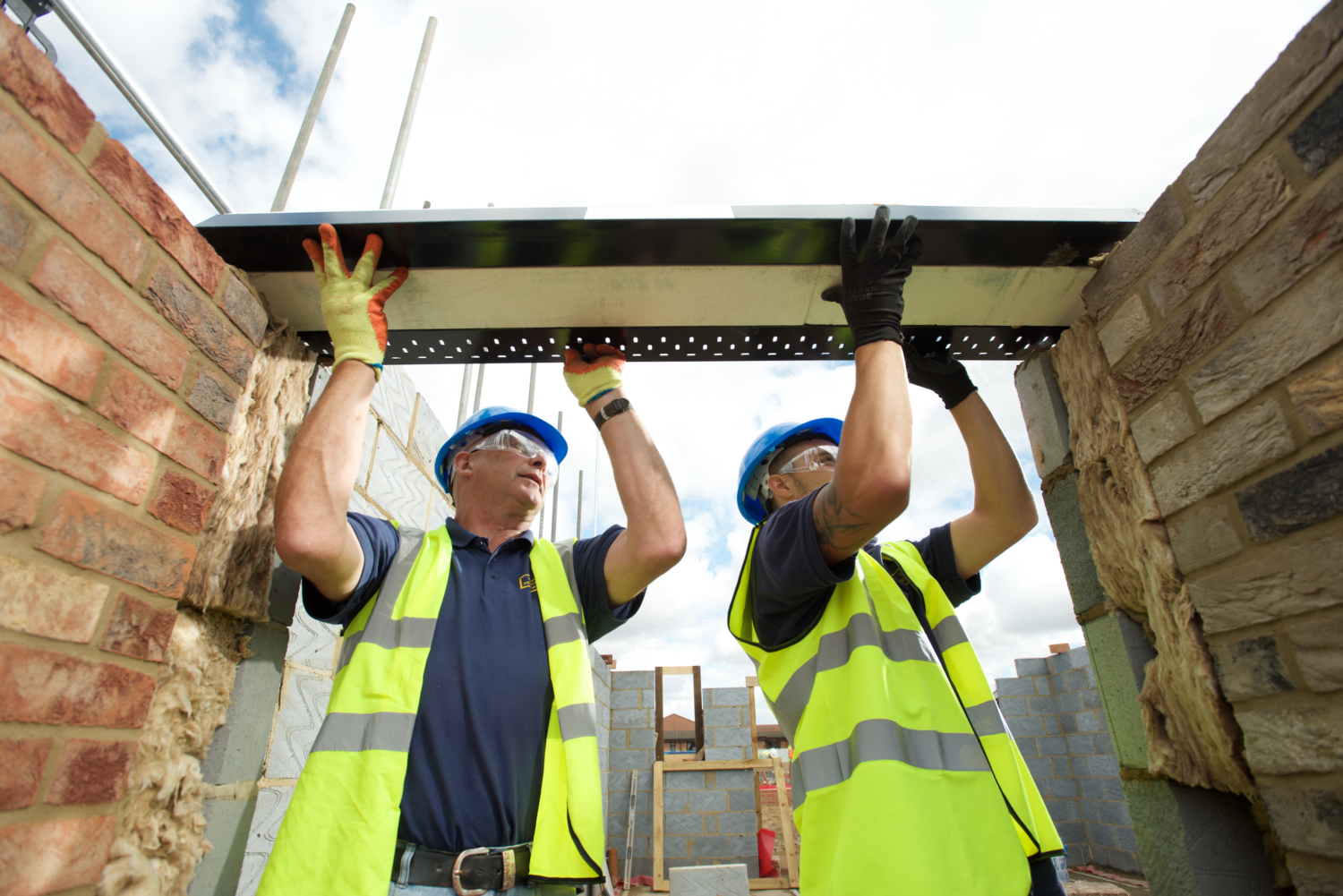
Anyone with an eye on Fabric First, or indeed steel lintels specifically, will not have failed to notice the new generation of lintel design to hit the market. Here Catnic’s Technical Director Richard Price assesses their impact and considers how and why to specify the best lintels for optimal performance.
Interestingly the heat lost from the UK’s average building stock has been reduced by 23% since 1970 as a direct result of the efforts to address and improve building energy efficiency (Palmer & Cooper, UK Housing Energy Fact File, 2013).
According to the Energy Saving Trust, about a third of all heat lost in an uninsulated home escapes through the walls. Because heat always flows from a warm area to a cold one, surfaces that facilitate this represent weaknesses in the building’s design. Known as thermal bridges, they not only result in colder indoor environments, interstitial condensation and issues with damp but also increased heating and cooling demands, energy costs and CO2 emissions. They are frankly the building specifier’s nemesis when it comes to the increasingly complicated demands of the Fabric Energy Efficiency Standard, Part L and SAP compliance.
This means wall detailing and the elements of the wall that represent the potential for thermal bridging must be carefully considered in order to achieve the optimum energy performance for the building. The thermal performance of a building is calculated by taking into account heat loss through the fabric of the building itself, such as walls, roof, floor, doors and windows, and through linear thermal bridges found at junctions between different elements of the building including window heads, jambs and cills.
With more than 10,000 lintel variations to select from, the correct choice of lintel depends on a variety of factors including building location, construction type, loadings and the required thermal performance. Unquestionably there will always be more than one right answer. In turn this leaves the building designer with the conundrum of balancing psi values against structural performance criteria, cost and practicalities of use.
Of course actual lintel specification only goes so far; design performance can only be achieved in practice if the products are installed correctly. Considering all steel lintels have to be CE marked, in accordance with BS EN 845-2:2013+A1:2016, it is easy to see how the specifier may simply opt for a generic ‘equal or equivalent to’ specification when it comes to the new generation of ‘thermally broken lintels’ on the market.
However, there is a solution that offers a simple specification choice, marrying structural excellence with the performance criteria requirements of Appendix Q in SAP 2012, providing easier compliance with Part L and reducing heat lost through window head details by 96%. It is a thermally broken steel lintel that delivers an independently verified energy transmittance psi value of 0.02 to 0.05 W/mK available in a composite, site-practical design.
Safe working loads are vital to building integrity. For lintels EN 845-2 and EN 846-9 are the critical compliance standards. Reassessing loads over lintels according to the building type and materials is time-consuming. Therefore a lintel solution that comprises safe working loads within these parameters offers a simple conversion for specifiers and design engineers. Site readiness and ease of use and handling play a part too. With no need for propping onsite thanks to their composite design, such lintels can be installed in the same way as standard cavity wall lintels.
Each of these features represents time, cost and importantly energy savings for specifiers. By ensuring thermally broken lintel selection encompasses structural performance, thermal performance and ease of use, the most robust specification for cavity wall design and performance will be achieved.
More
-
- SolarSeam
- Urban
- Sustainability
Catnic Supports Future Homes Standard Following SolarSeam’s London Launch